搬送自動化コラムvol.4
AMR導入後では遅すぎる。
導入前に知っておくべき安全の国際規格「ISO3691-4」
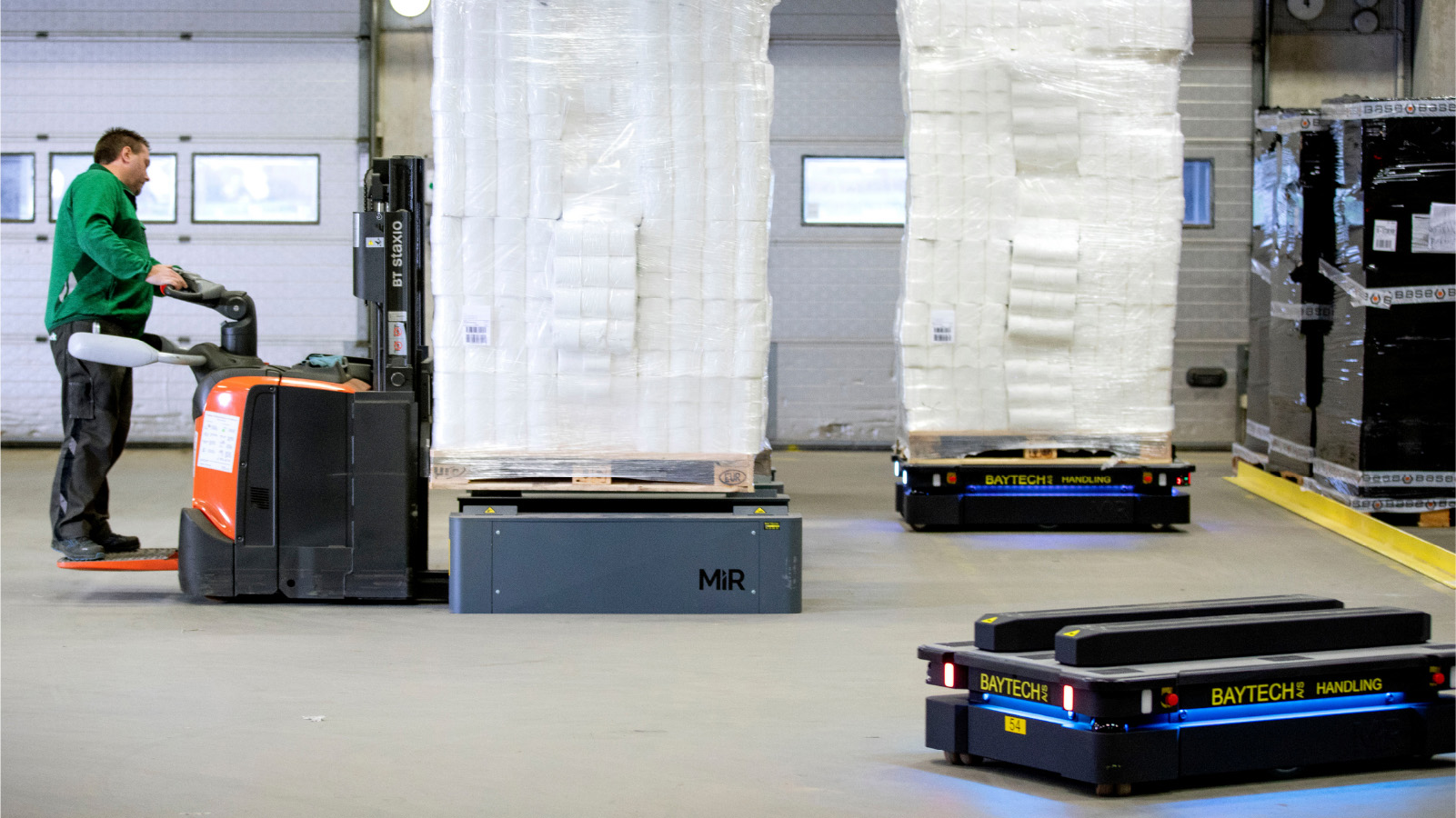
目次
安全の国際規格、「ISO3691-4」をご存知でしょうか。
私たちIDECファクトリーソリューションズが運営する協働ロボット.comでも、何度かウェビナーやダウンロード資料で紹介してきた「ISO3691-4」。すでにご承知の方も多いのではないかと推測しますが、まだという方のためにあらためてご説明します。
AGVやAMRなどの無人搬送車が走行する区域は、作業者の作業場所や歩行区域と重なることが多く、安全性の確保が重要になります。
そのため安全に関する国際規格のC規格(個別機械安全規格)では、産業ロボットと同様に、無人搬送車や無人搬送車システムの安全性確保に関する要求を定めています。それがISO3691-4です。
ISO3691-4:Industrial trucks – Safety requirements and verification –
Part 4: Driverless industrial trucks and their systems
この規格には、無人搬送車に実装すべき安全機能や、システムとして運用する際の安全確保の手法がまとめられています。
ISO 3691-4は、2020年2月に初版が発行され、2023年6月に第二版が発行されました。 また、ISO 3691-4第1版はJIS化されてJIS D 6802:2022として発行されています。ただし、技術要求が変更されている部分があるため、内容が完全に一致しないので注意が必要です。
ISO 3691-4:2023の対象範囲
自動運転するように設計されている動力付無人搬送車両とそれらを複数制御して運用する無人搬送車システムが対象となります。
無人搬送車としては、ISO 5053-1で定義している人が運転する産業車両を自動化した車両タイプや、“AGV”、 “AMR”、 “bots”、 “automated guided cart”、 “tunnel tugger”、 “under cart”などがあげられます。
ただし、機械的手段(レール,ガイドなど)によって誘導される車両や、人が必ず操作する必要がある無人搬送車とみなされないリモートコントロールの車両は適用外です。
代表的な危険源・危険事象のリスト(ISO 3691-4 付属書Bより)
無人搬送車システムの安全化にリスクアセスメントは不可欠です。特に重大な事故につながる危険源・危険事象を抜け漏れなく同定することは非常に重要です。なぜなら、この段階で同定できなかった場合、重大事故が発生する可能性のあるシステムを運用することになるからです。
ISO3691-4では、付属書Bに無人搬送車や無人搬送車システムに関する重要危険源リストが用意されています。このリストは、ISO12100の付属書Bにあるリストと同じ分類となっており、機械的、電気的、人間工学原則無視など、様々な視点で危険源・危険事象の同定ができるようになっています。また、危険源・危険事象に対する方策もISO3691-4にある項番が記載されており、リスクアセスメントからリスク低減方策が対応できるようにまとめられています。
「ISO3691-4」について概略をご理解頂けましたでしょうか。
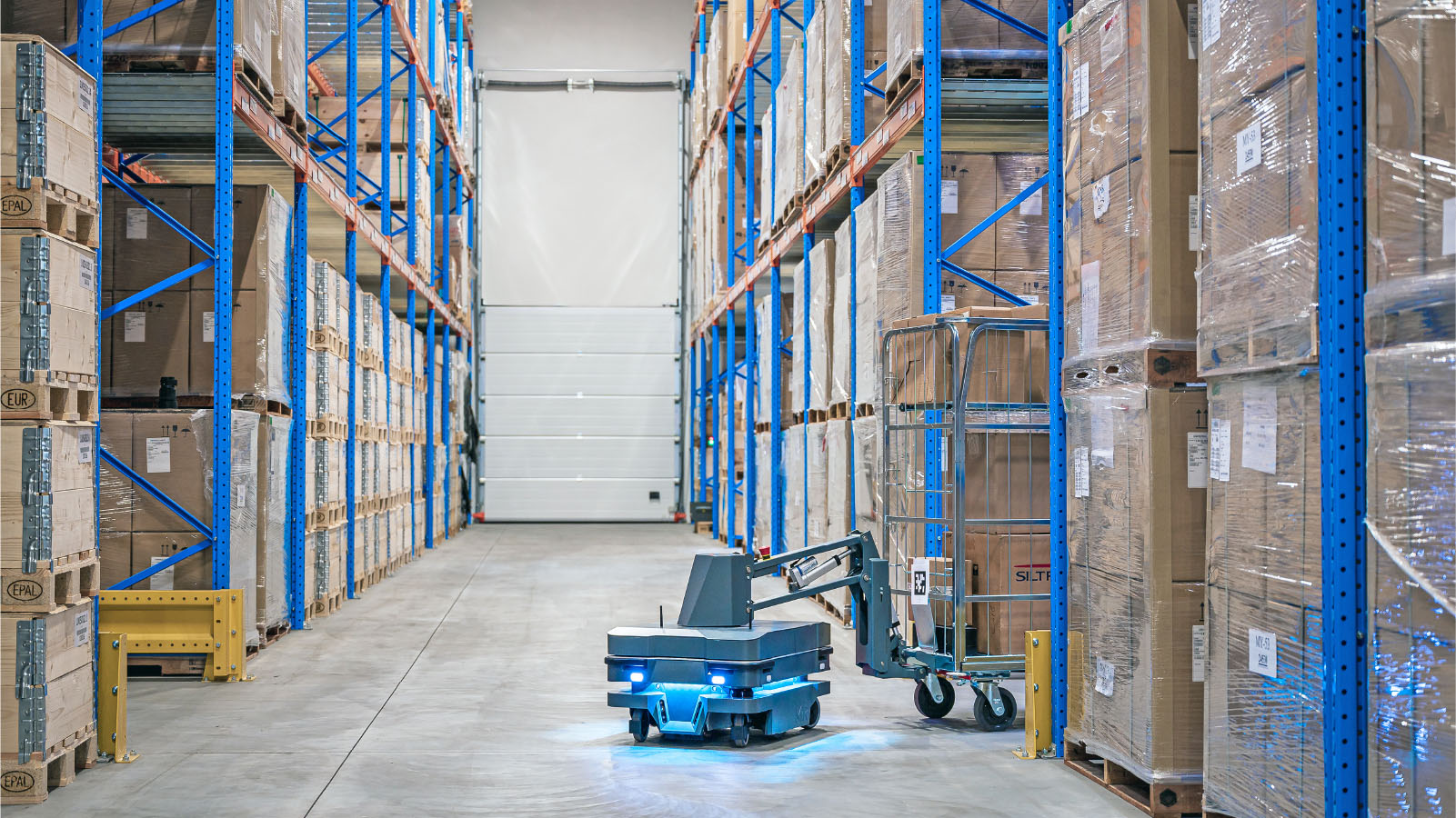
「ISO3691-4」を知らないまま
導入してしまった際のリスクとは
それでは「ISO3691-4」を理解しないまま、AMRを導入した場合、どんなリスクが想定されるのでしょうか。考えてみましょう。
「ISO3691-4」を知らないまま、AMRを導入した際の以下のようなリスクが考えられます。
想定されるリスク
- 規格で要求される構造を無視したAMRを導入してしまい、重大事故(荷の落下による押し潰し、足をひかれる)が発生するリスクが生じる
- 想定している運用に必要な安全機能を備えていないAMRを導入してしまい、重大事故(人と衝突する)が発生するリスクが生じる
- AMRシステムを運用する際に、走行するルートの環境に応じた適切なルートや速度に設定されず、重大事故(人と衝突、壁などとの間に人が挟まれる)が発生するリスクが生じる
- 残留リスクに対する効果的な手法を実施できず、重大事故(人との衝突)が発生するリスクが生じる
具体的な重大事故の例
- 人検出用のセンサに汎用センサを使用しており、機器故障が発生した場合、人を検知できず衝突
- AMRに作業者が足を轢かれて骨折
- AMRから落下した搬送物が周辺にいた作業者に接触し負傷
- 残留リスクとなる人の飛び出しによる衝突を回避できずにAMRと衝突
結果として何が起きるか
- 事故や怪我の発生リスクの増加
安全な運用を人に依存することになるため、事故や怪我の発生リスクが増加する - 生産性の低下とコストの増加
事故により業務が停止し機会損失が発生する可能性が高まる
損傷した設備や機械の修理・交換にコストがかかる - 法的責任と罰則のリスク
労働安全衛生法によるリスクアセスメントに基づいた設備安全化の要求が存在するため、事故が発生した場合、法的責任を負うリスクが増加する
刑事罰や罰金、営業停止、訴訟のリスクが増加する
企業の信用と評判の失墜が生じるリスクが増加する
上記のように、AMRを自社の工場や倉庫で運用する際には、規格に準拠し安全を確保することが前提となりますので、導入担当者は、導入前の早い段階で「ISO3691-4」の内容を理解しておくことが必要不可決です。
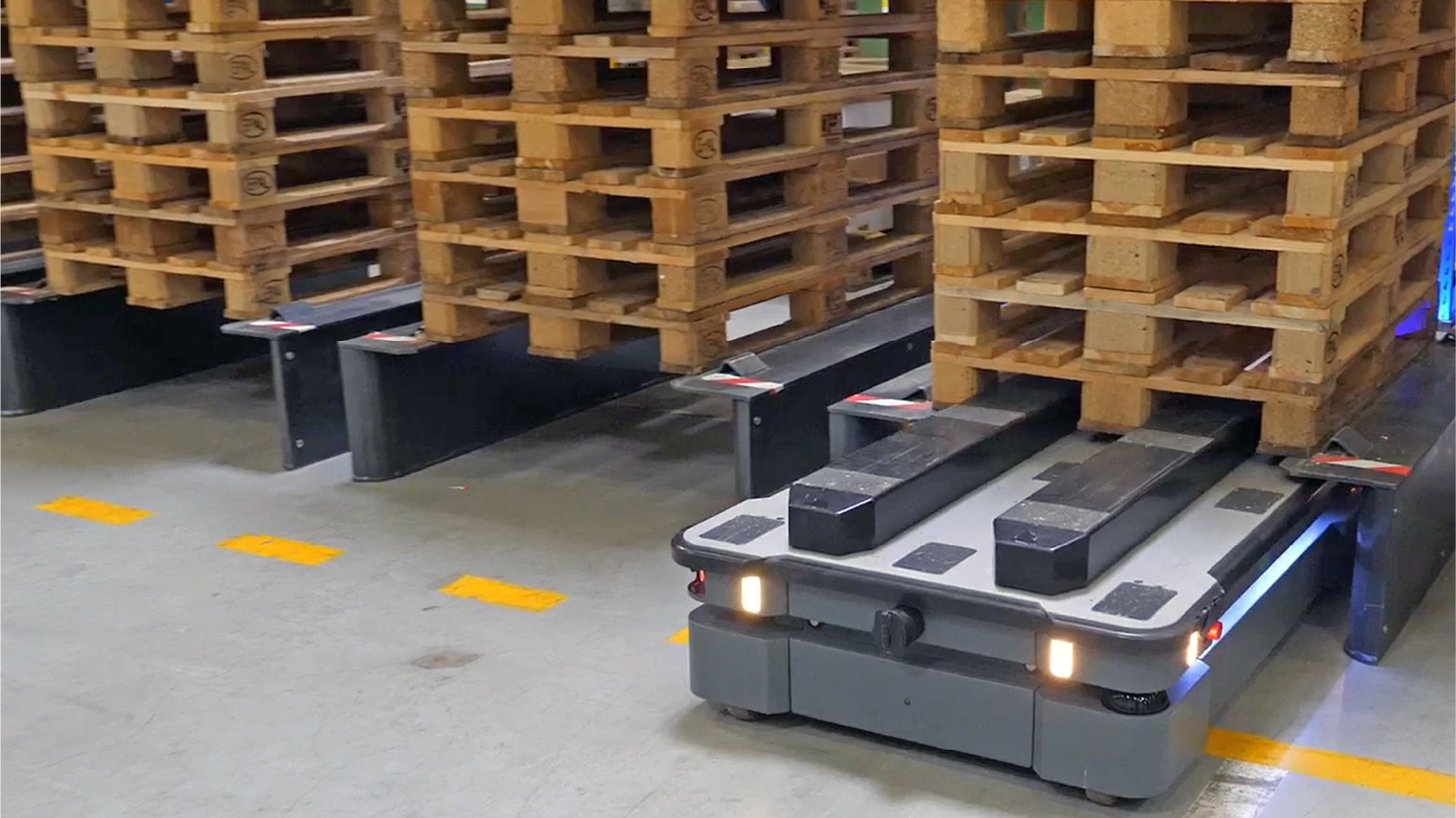
AMRシステムの一般的な構築プロセス
それではAMR導入によるシステム構築プロセスのどの段階でどんな知識が必要となるのか、見てみます。AMRシステムの一般的な構築プロセスは以下のようになります。
導入までのステップ
1システム化要求仕様の明確化
●主な内容
・搬送対象(荷物・資材)の特性把握
・搬送ルート、停止箇所、台数、搬送頻度などのニーズ把握
・工場・倉庫レイアウトと人的作業の動線確認
・安全要件や社内ルール(歩車分離の可否、警報の要否など)の確認
・設備配置変更の可能性の確認と最適ルートの選定
・AMRに必要な安全機能の決定
この段階ではまだ具体的なリスク評価や設計には至りませんが、「どこまでの安全対策が必要か?」という方向性を定めるため、ISO 3691-4の概要を理解しておく必要があります。
2AMRの選定とトップモジュールの構想設計
●主な内容
・AMRメーカの比較検討(ナビゲーション方式、センサ仕様など)
・トップモジュール(カート牽引、リフター、コンベアなど)の構想設計
・上位システム(WMSなど)とのインタフェース要件定義
この段階では、検討しているAMRのセンサ構成(経路内の人検出)やブレーキシステム、速度制御などがISO 3691-4の安全要求を満たしているかという視点が重要になります。
3トップモジュール詳細設計
●主な内容
・トップモジュール(ワークハンドリング部)の構造・動作設計
・制御シーケンス、非常停止や動作インターロック設計
・接触リスクや挟まれリスクの評価
ここでリスクアセスメントが必要になります。ISO 3691-4では、AMRのみだけでなくトップモジュールや周辺機器・設備も含めたAMRシステムとしての安全設計が求められています。
ISO 12100(リスクアセスメントの基本規格)の知識や、要求パフォーマンスレベル(PLr)に基づいた制御回路の設計検討も必要になります。
4搬送ロボットシステムの組立(トップモジュール、カートなどの製造組立)⇒初期設定
●主な内容
・部品の組立や配線
・制御ソフトの初期設定
・非常停止ボタン、人検出センサの動作確認
・バンパー、ライト、ブザー等のテスト
センサ類の死角がないか、安全機器が正しく動作するか、その他の要因がリスクを高めないかなどをチェックします。
5現地納入、マップ作成、走行ジョブ作成、走行調整
●主な内容
・実際の作業環境に合わせたマップ構築
・周辺設備、上位システムとのジョブ連携設定
・減速ポイント、待機エリア、侵入禁止エリアの設定
・安全性確認(人的接触や混在・環境でのリスク評価)
実際の現場にて、AMRの走行マップを作成し、ジョブの定義(搬送開始点・終了点、トリガー条件など)を行います。走行ルートや優先順位、交差点での動作も調整します。
その上でリスクアセスメントを行い、マップ上での速度制御ゾーンの設定、周囲に人が多いエリアでの速度制限や進入禁止設定、保守作業時の手順などを決定します。
6システム稼働
●主な内容
・引き渡し、オペレーション教育
・運用中のエラー検出と対策
・点検やリスク見直しの体制づくり
システム稼働後も、教育用の安全運用マニュアルの作成、定期的な点検と記録の保管、ソフトウェア更新や構成変更に伴うリスクの再評価などが必要です。ISO 3691-4はAMRシステムの導入時だけでなく、運用中も必要になる規格だといえます。
いかがでしたでしょうか。設計の段階から「ISO3691-4」を理解した上で導入を進めることで、安心してAMRを活用することができます。
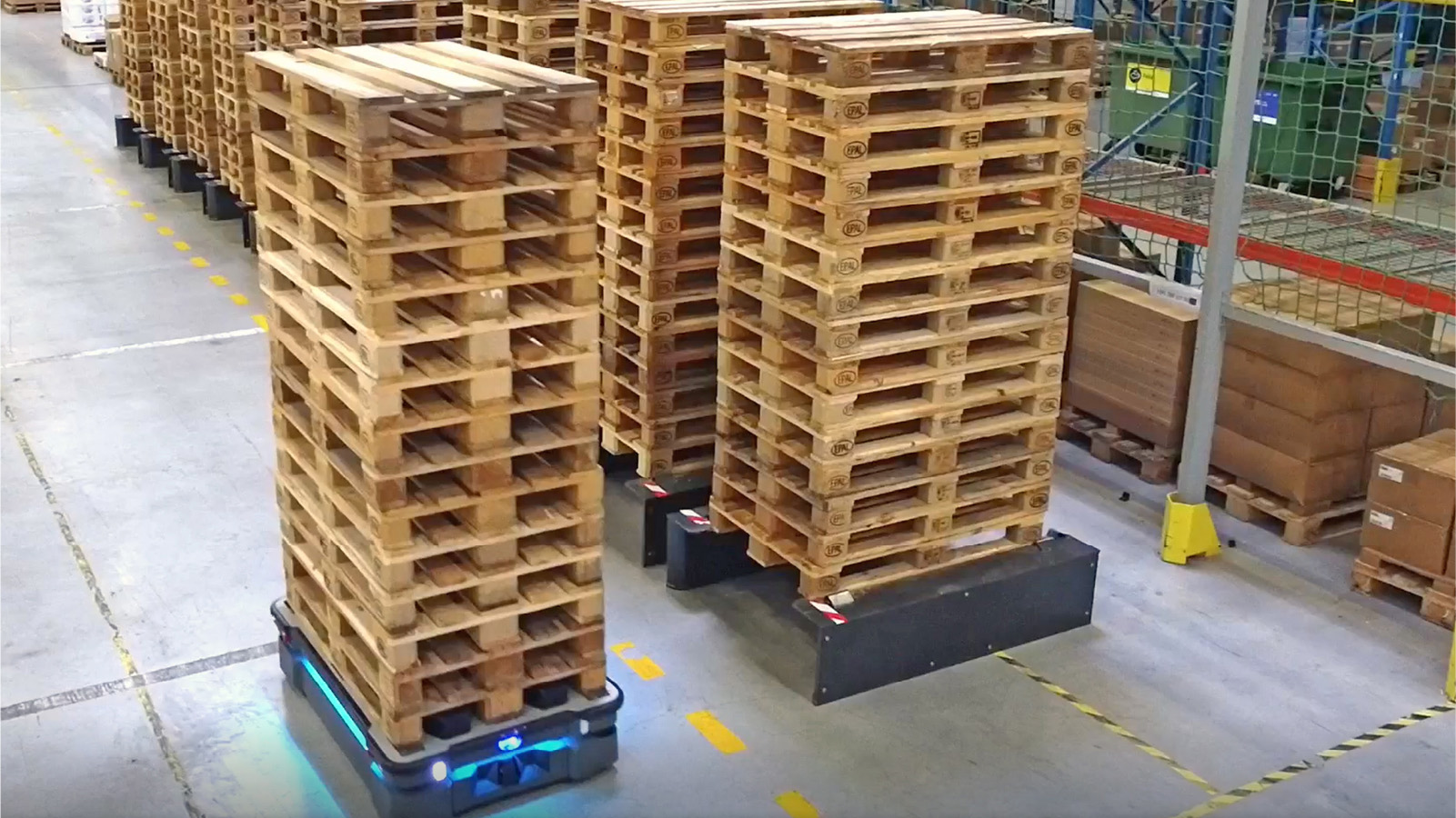
安全の専門家が在籍。導入・運用時の安全安心を担保する
ロボットSIer(システムインテグレータ)の役割
設計の段階から「ISO3691-4」を理解した上で導入を進めるメリットを先ほどお伝えしましたが、なかなか自社だけで導入を完結させることは難しいところがあります。そんな時にお役に立てるのが、私たちのようなロボットSIerです。
ロボットSIerの一般的な役割
ロボットSIerは、ロボットの導入や活用をサポートする専門会社で、次のような役割を担います。
- ロボットの導入を検討する企業の現場課題を分析し、最適なロボットシステムを構築する
- システム全体の導入提案、設計、組立、立上げなどを行う
- ロボットの選定や導入、運用まで幅広くサポートする
- 現場作業員の安全の確保やアフターサービスのメンテナンスを行う
ロボットSIerは、主にロボットメーカ系と独立系の2つに大別されます。
- ロボットメーカ系は、大手電機メーカなどロボット取り扱い企業によるSIer事業で、大規模なプロジェクトを得意としています。
- 独立系は、大手電機メーカなどとの資本関係を持たないSIerで、中小企業が多く、得意分野に特化しています。
ロボットSIerの活用には、次のようなメリットがあります。
- ロボット導入までの時間を大幅に短縮できる
- 現場の予算・規模感にあったロボット導入を提案してもらえる
- 消耗品を提供してもらえる
- ロボットの運用に精通した人材を派遣してもらえる
- ロボットの運用データを分析し改善提案をしてもらえる
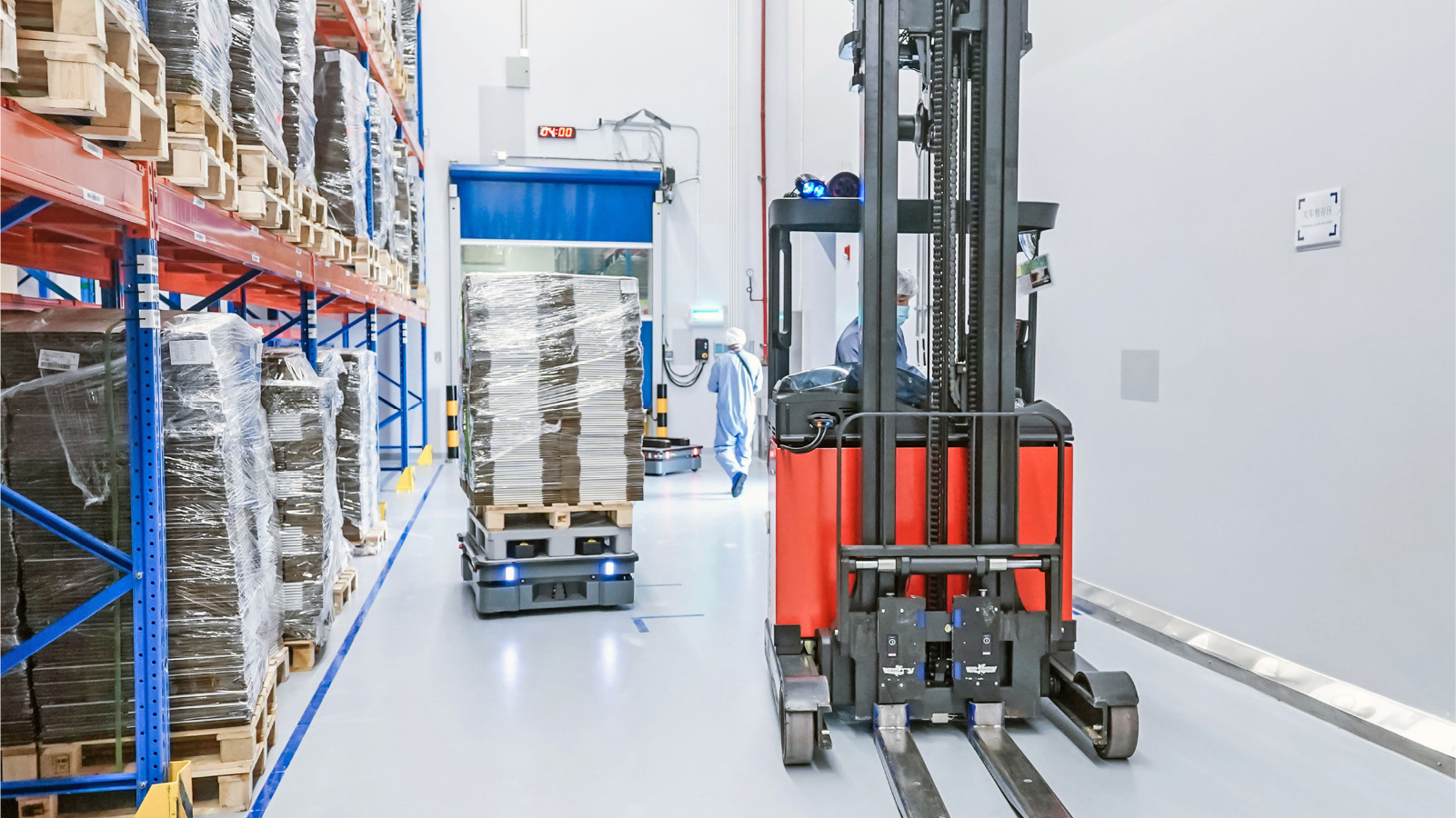
人と共存するAMRシステム構築における
ロボットSIerの重要性
作業員とAMRの協働作業空間である限り、技術的に十分にリスク低減ができない残留リスクが存在します。
AMRに関しては、人検知機能は作業者との接触防止のために重要ですが、安全機能として、静止した進行方向の作業員を含む障害物に対して接触しないように車両を停止させる必要があります。
ISO3691-4の試験は、AMRの進行方向の静止している障害物に対して衝突する前に停止することであり、車両に向かってくる人、側面から飛び出してくる人に対しての衝突回避まで求めていません。これは、技術的にも止めることができず、現状の安全機能の限界です。
ということは、人との協働作業空間で運用するAMRの残留リスクには、AMRに向かってくる作業員、側面から飛び出してくる作業員への衝突が含まれることになります。
この残留リスクの低減には、設備として車両の警告音や警告灯、運行区域の視認性と走行路の明示が挙げられますが、人とAMRの切り分けがありませんので、作業者側の教育・訓練による危険事象の回避も必要となります。
これらは、設備制作側(SIer、ロボット)と設備運用側(ユーザ)の間でリスクコミュニケーションを図りながら最適な運用ができるように進めなければなりません。
まとめ
生産性と安全性の両立を実現するためには、「ISO3691-4」に適合した上でいかに生産性を高めるシステムを設計するかが鍵を握っています。そのため、できればAMR導入前のシステム設計の段階から規格を熟知したロボットSIerと連携していくことが望ましいと考えます。
当社には「ISO3691-4」に長けた専門家が在籍、お客様の状況や環境に合わせて、設計から機種選定、導入。さらには導入後の運用までサポートしています。お気軽にご相談頂ければ幸いです。