Case Study of DX Promotion当社製造DX推進事例
EPLAN活用
「制御盤筐体加工工程での省時間化」によるコスト削減
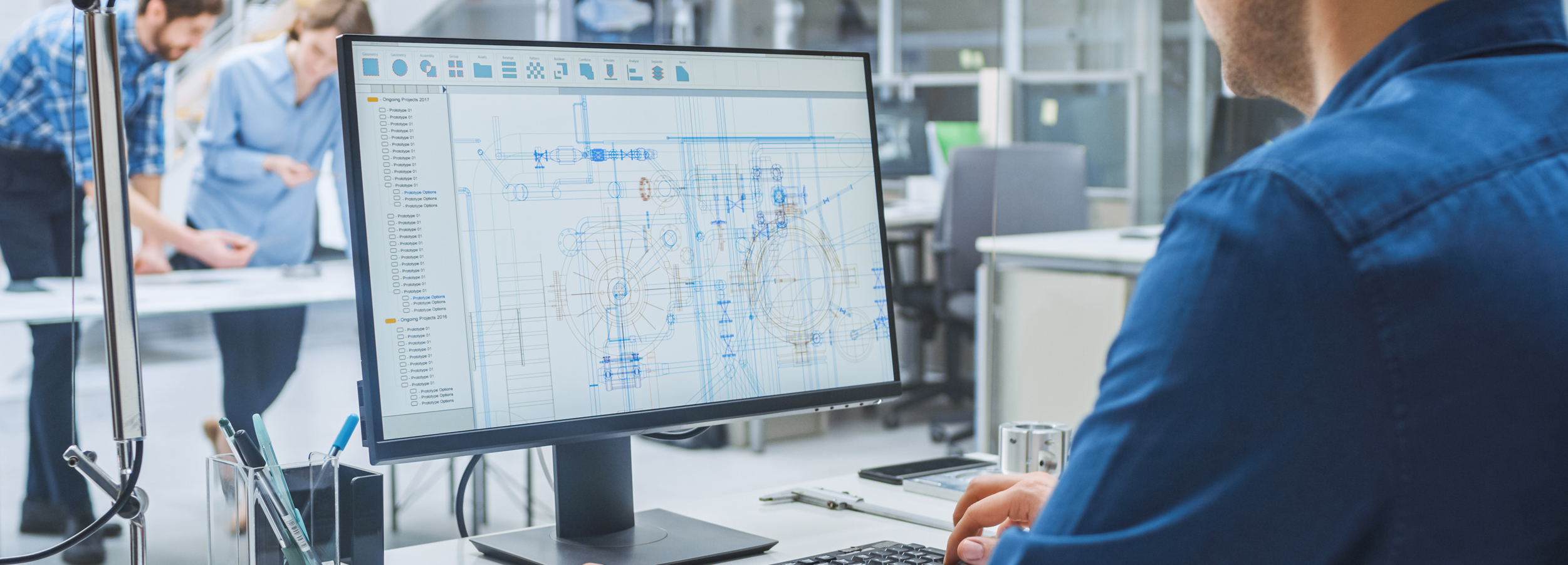
●活用前
制御盤のエンクロージャのドイツのRITTAL(リタール)製品への穴加工に際して、
従来は、まずECADやAutoCADで外形・配置図の設計を行い、さらに板金展開図を作成した上で、
板金加工業者との打ち合わせやデータの種類の調整、専用図の作成などにより、多くの時間を費やしていました。
社内のDX推進のプロセスでは、このような無駄な設計工数を削減し、業務効率化を図ることが課題でした。
●活用後
当社では2020年に統合型電気CADのEPLAN P8とPro Panelを導入、それを用いて設計業務の効率アップを模索していました。
約半年間のウォーミングアップ期間を経て、適切なセットアップを実施することにより、
EPLAN上で各種制御機器を外形図に配置するだけで穴加工図の自動作成が可能となりました。
ウォーミングアップ期間では、部品データの登録を高いレベルで的確に実施。この作り込みにより、初めて効率的な業務が可能となりました。
逆に、ここに時間が割けない場合、制御盤のDXは難しいこともあらためて実感しました。
EPLANの思想ではRITTALと連携するところまでは通常の製造フローの一つとなることから、そのデータの作り方と使い方が肝となります。
上記のとおり、当社内でEPLANをフル活用できるようになったことから、従来の板金加工業者ではなく、
RITTAL JapanにEPLANデータをもとにした加工依頼を直接出すことが可能になりました。
●活用効果
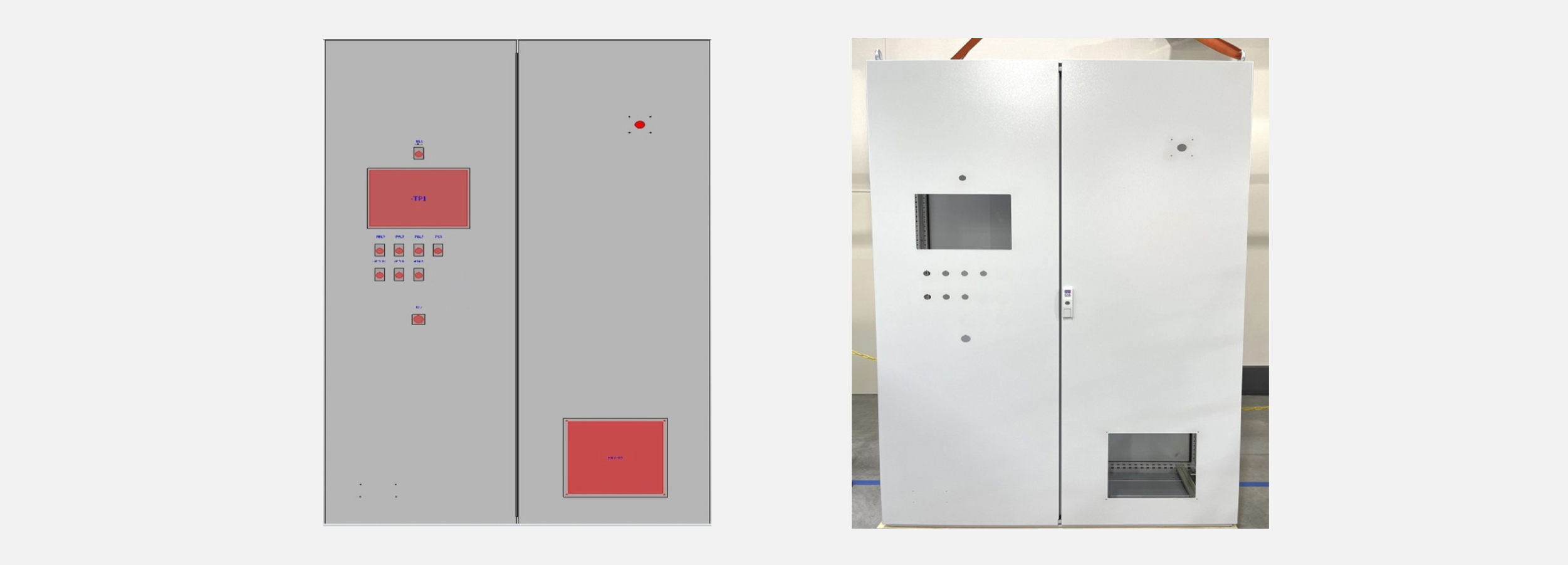
- ●指示、伝達時間の削減
- ●既製品への筐体への穴加工時の品質の担保
(傷・スパッタの飛び散りなど) - ●設計工数の削減
(設計者は従来比:1/2程度 調達管理者はその時間そのものがゼロに) - ●加工コストの削減
- ●人的ミスの削減
RITTAL JapanでのEPLANのデータをもとにした加工・組立の依頼に変更することにより、指示・伝達時間の削減、既製品への筐体への穴加工時の品質の担保(傷・スパッタの飛び散りなど)が実現できました。
特に板金加工フローで設計者と調達担当者が拘束される時間が大きく減る(設計者は従来比:1/2程度、調達管理者はその時間そのものがゼロに)ことにより、設計工数の削減が可能となりました。
普段数値化されにくいものが明らかに削減できています。
さらに、RITTAL製品への穴加工コストも従来の板金業者での加工よりも削減できました。
以上をまとめると、コスト、時間、人、破損リスクなど複合的な面でのコストダウンと同時に人的ミスの削減による品質向上をはかることが可能となりました。
補足情報
EPLANデータを用いてRITTAL製の箱の購入から加工までを一元化している制御盤メーカーは日本国内でIDECファクトリーソリューションズ1社のみ(2021年10月1日現在、RITTAL JAPAN調べ)であり、世界標準となりつつあるEPLAN・RITTALと連携をし、そのシステムを最大限活用できる国内でも数少ない制御盤メーカーです。