搬送自動化コラムvol.1
自社の搬送工程自動化に適するのは、AGVかAMRか?
生産性向上に必要なのは全体最適の視点
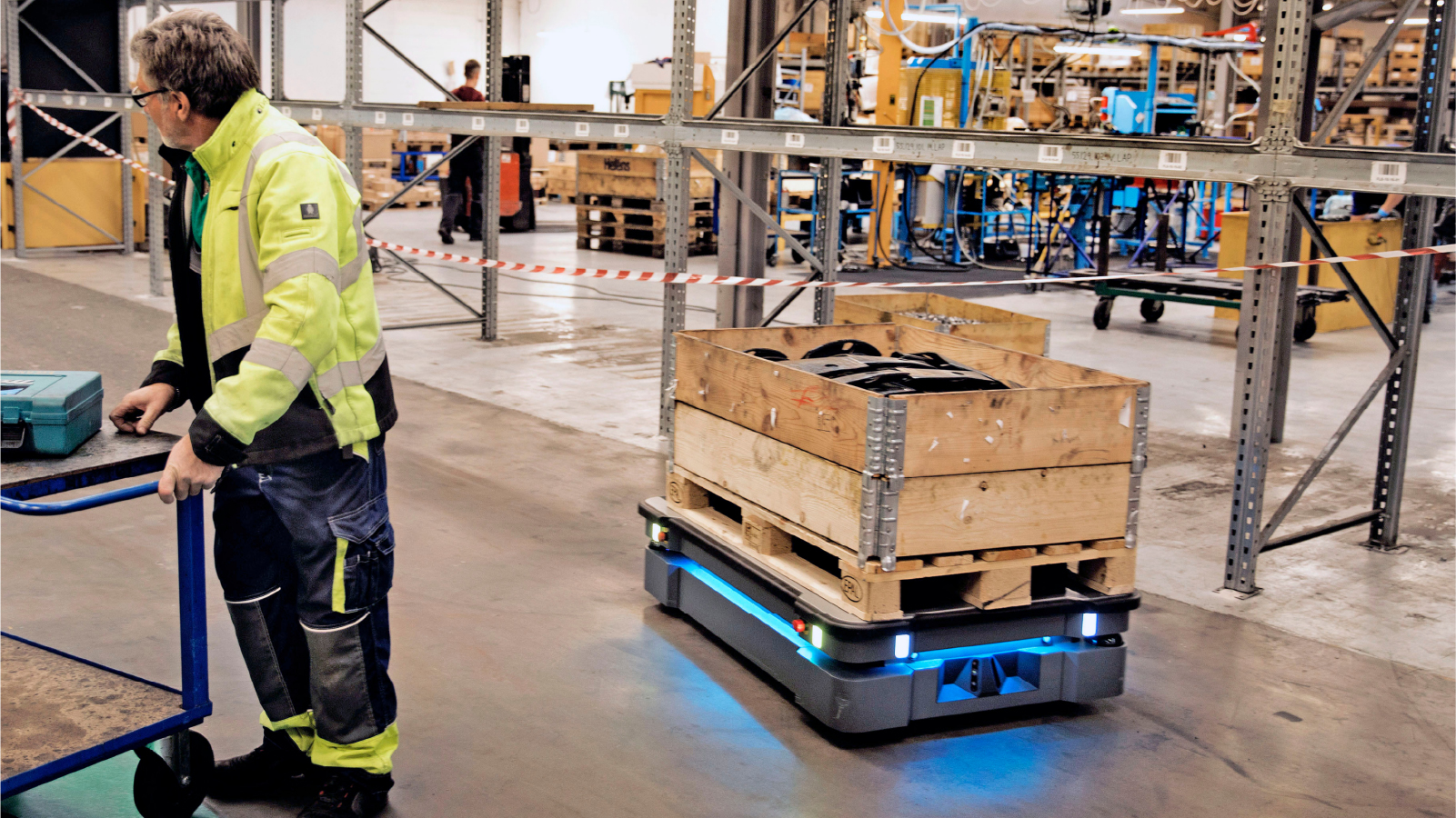
高機能であっても使わない機能は必要ない
商談の際、お客様の中には最初からAMRありきで自動化の話を進められる方が一定数存在します。
もちろん当社が販売するAMRを購入してもらうことは嬉しい限りですが、とはいえ、AGVで済む自動化であれば、一般的にAGVと比較して費用が高く、高機能すぎるAMRを選択する必要はありません。
(それでもAMRを選ぶ理由は確かにありますが、それはまた別の記事で紹介します)
家電のリモコンにボタンがどんどん増えていった結果、高機能であることが良いことだと、使わない機能が搭載された家電をとりあえず購入する生活者が増えました。そんな経緯に似ているような気がします。例えは悪いですが、必要のない機能はどんなに高機能であっても宝の持ち腐れになります。
自動化の担当者として、まず必要になるのはAGVとAMRの違いを正しく認識することではないでしょうか。話を進める前にざっとおさらいをしておきます。
予め知っておきたい、AGVとAMRの違い
AGV | AMR | |
走行方式 | 誘導走行(誘導体が必要) | 自律走行(誘導体不要 ガイドレス) |
移動範囲 | 固定されたルート | 自動算出したルート |
人との協働 | 不可 | 可 |
障害物への対応 | 停止 | 回避、再ルーティング |
はじめに理解して頂きたいのはあくまで「AGVは車両。AMRはロボット」という概念の違いです。
AGVは搬送台車とも呼ばれるように、A地点からB地点に物を移動させるための搬送車両です。それ以上でもそれ以下でもありません。対してAMRは自律的に判断して移動することができるロボットです。
特徴的なポイントについて、詳細に見ていきます。
走行方式
AGVとAMRの最も大きな差、それは走行方式にあります。 走行方式の違いがそのままAGVとAMRの区分、定義になっているほどです。
AGV
AGVは automatic guides vehicle の略称。日本語では無人搬送車や自動搬送車と呼ばれています。JISD6801では、AGVを「一定の領域において、自動で走行し、荷など人以外の物品の搬送を行う機能をもつ車両で、道路交通法に定められた道路では使用しないもの」と定義。あくまで車両という位置付けです。
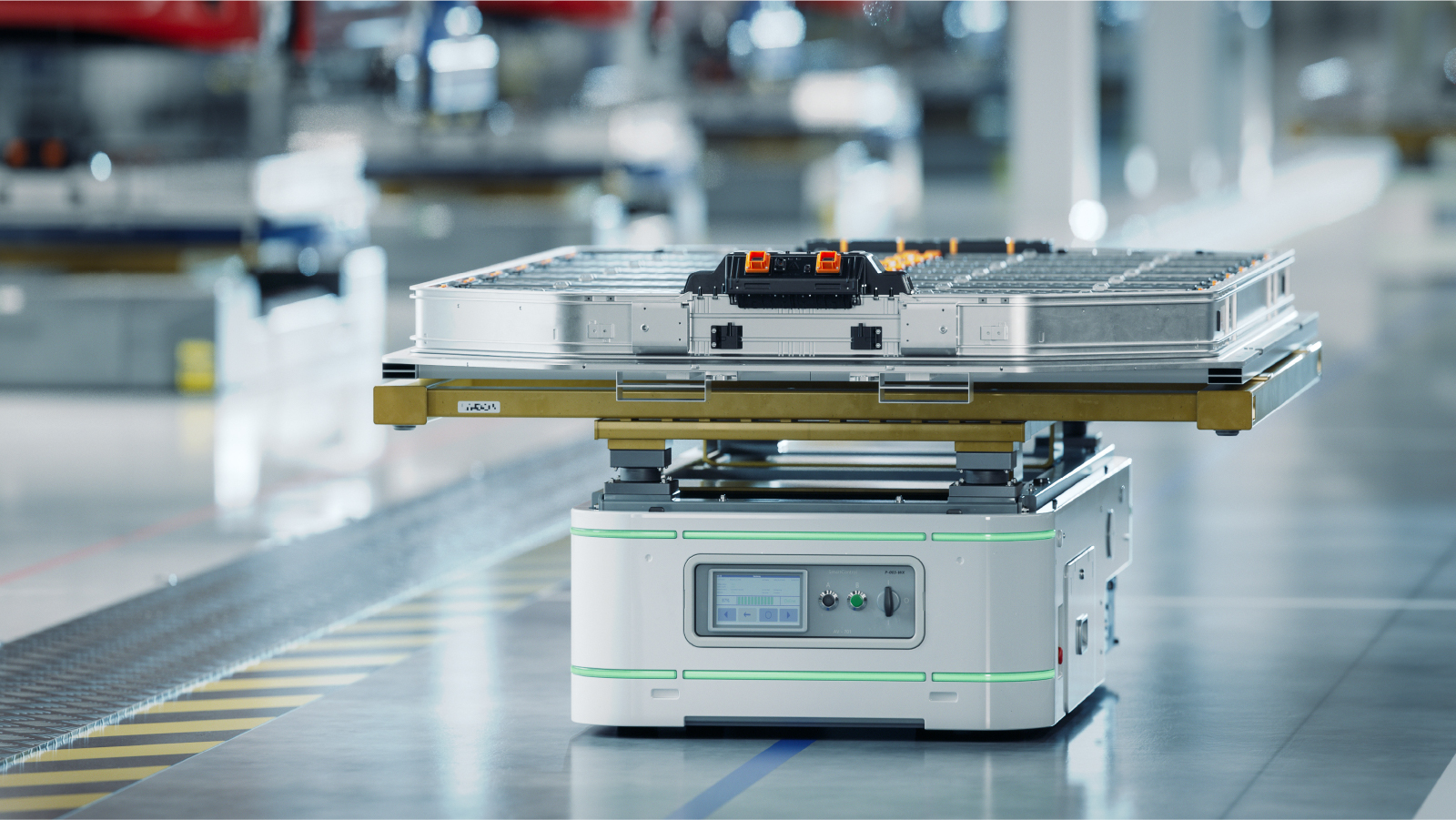
AMR
AGVの中でも、磁気テープなどの誘導体を必要とせず(ガイドレス)で、搭載されたセンサなどの情報から自己位置の推定を行うものが、一般に AMR(autonomous mobile robot)とされています。日本語では、非ガイド走行方式 AGVや次世代AGV、自律走行搬送ロボットと呼ばれています。決められた条件内で走行するクルマという概念が進化して、自ら判断して移動するロボットになったと考えてもよいのではないでしょうか。
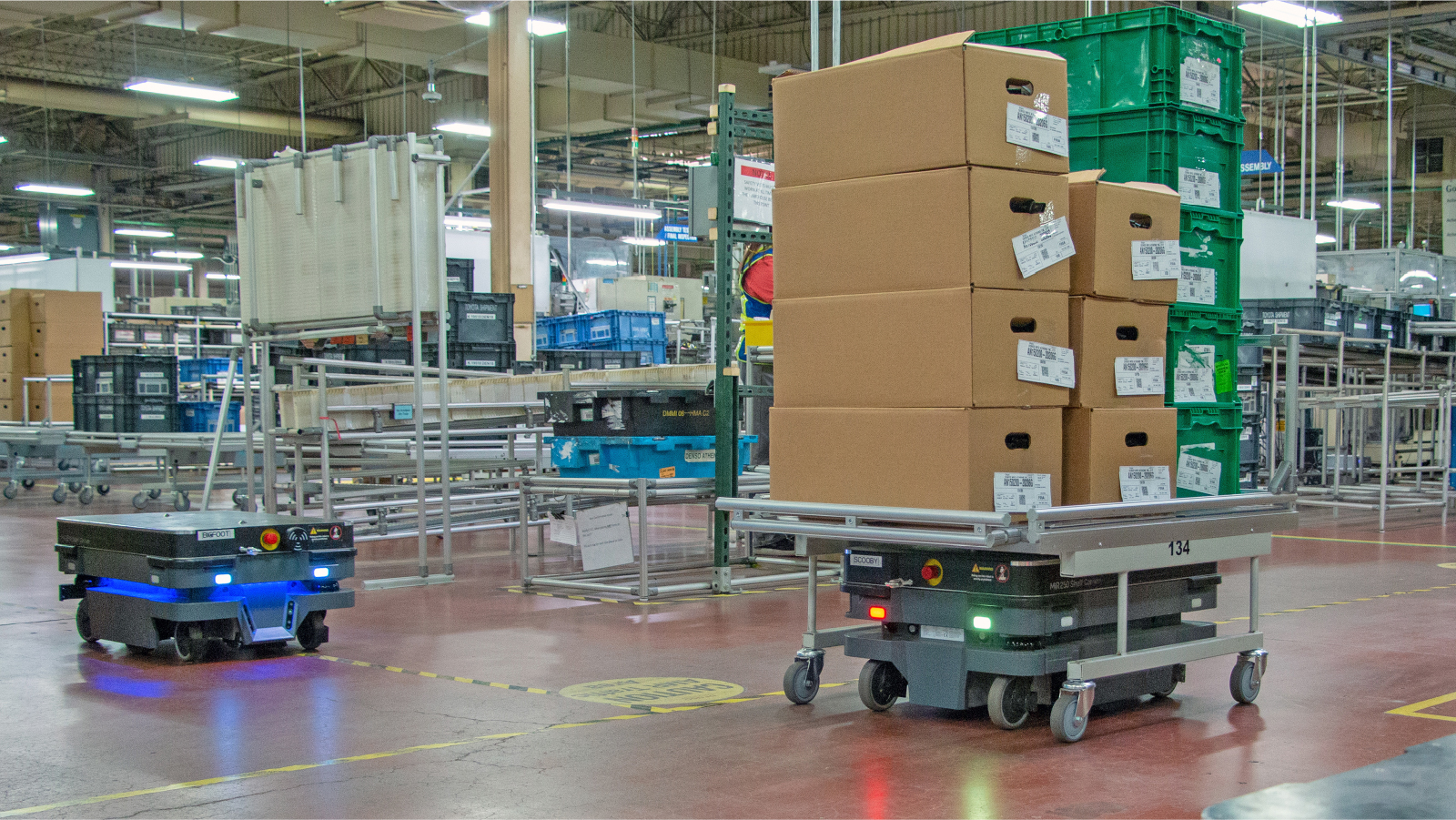
移動範囲
AGVとAMRは走行方式の違いにより、移動する範囲にも違いが生じています。
AGV
これまで述べてきたように、AGVは磁気テープなどの誘導体によって設定された固定のルートを走行します。そのため誘導体が設置されていない場所での走行は不可能で、固定のルート上に障害物があった場合は停止し、走行ができなくなります。作業に支障なくスムーズに走行させるためには、障害物のない場所の確保及び誘導体の設置が必須の条件となります。
AMR
一方、AMRは周囲の環境に合わせて自動算出したルートを走行します。そのため走行ルート上に人や障害物がある場合でも、回避もしくは減速で対処が可能です。磁気テープなどの誘導体の設置が不必要(ガイドレス)なことから目的地の変更も容易で、状況に合わせて変更ができます。これにより、今までAGVが導入されたことのないような、新しい場所への導入が可能となりました。
いかがでしょうか。ご理解頂けましたでしょうか。
かつて産業ロボットしか存在しなかった時代には、ロボットを柵で囲い、人と隔離して使用していました。そうすることで、人へ危害が与えられることなく、安全が担保された上で安心して使用することを可能にしました。
ただ、その分、特定の作業に限定され、人と一緒に何かを行う、いわゆる協働という作業には不向きでした。人は人、ロボットはロボット、切り分けられることによる限界がどうしても生じてしまいます。その限界を打ち破り更なる生産性を求める結果、開発されたのが柵なしで人との協働作業を可能とした協働ロボットです。もちろんその背景には法規制の改正などさまざまな追い風の要素がありましたが、技術の進化のプロセスにはよくみられる現象ではないでしょうか。AGVとAMRの関係もこれによく似ている気がします。
AGVとAMR。それぞれが適した現場とは
では、AGVとAMRの特性を理解した上で、それぞれが適した場面を考えてみましょう。
AGVで生産性向上が図られるシーン
- ・スピード重視の場所=タクトを重要視
- ・ルートが固定もしくは一定な場所
- ・一方通行の場所 、電車のような使い方ができる場所
- ・コンベヤの代替(コンベヤに柔軟性を求めると場合にAGVが選択肢になる)
AMRの方が生産性向上が図られるシーン
- ・工程内で複雑な搬送をしている場所
- ・待ち時間があってもよい、スピード重視ではない搬送
- ・タクトにはこだわらず、確実に次工程に荷物を届けたい
- ・ルートが変わる場所 、タクシーのような使い方ができる場所
- ・人の代替
- ・AGVなどで自動化できなかった部分をAMRで自動化
部分最適ではなく全体最適の視点で工場を俯瞰してみた時、
最も適した組み合わせがある。
物事をどれだけ高いところから見るか、どれだけ長い時間軸で見るか、役割や置かれた立場によって目線が違ってくるのは当然のことです。例えば、作業の専従者の目線ではいかに効率よく目の前の仕事をこなすか。対して生産管理の責任者であれば、いかに担当する製造部署が効率よく生産性を上げられるかの目線でしょう。
商談中に伺ったお話が象徴的です。
「こちらの製造ラインから次の製造ラインへの搬送を手動で行っているようですが、生産性を考えると、ここにAMRの導入を検討された方が良いのではないでしょうか」とお話ししたところ、「そうなると、当部署以外を巻き込むことになるので進む話も進まなくなる。」そんな回答でした。
つまりは部署が縦割りになっており、部署間調整が難しく、いわゆる隙間と言える部分に対しては自部署の関与が難しいという話です。このようなケースはおそらくこの会社に限ったことではないでしょう。
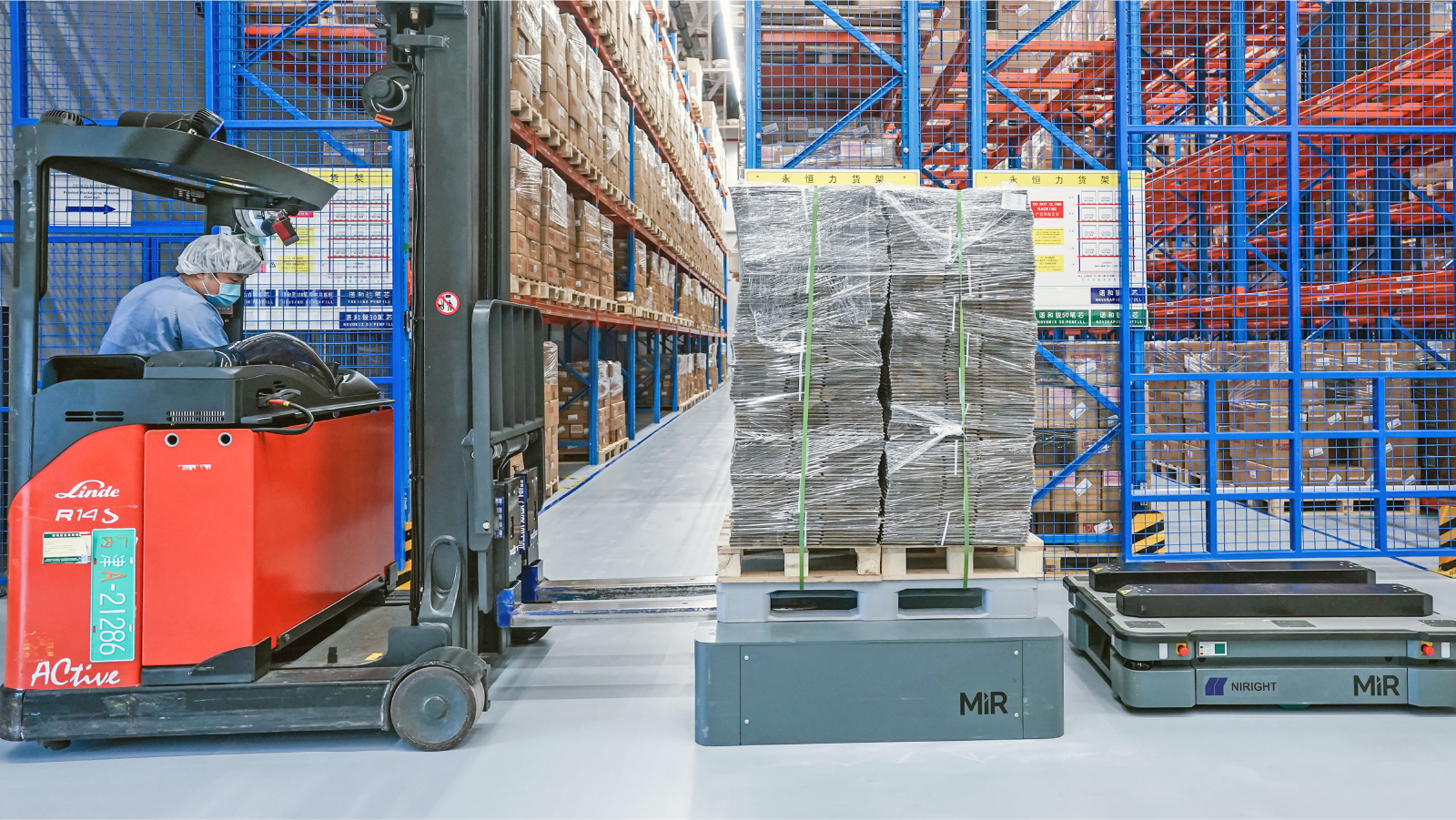
まとめ
重要になるのが、長い時間軸で俯瞰してみる経営者の目線
コロナ禍を契機に、人と人が非接触であることが大前提となり製造現場のあり方が大きく方向転換しました。この先、同様のことが起こるとも限りません。その時の備えは十分か。また現在、企業全体の課題でもある人手不足はこの先、解消されるのか。解消されないとしたら、人手不足を前提とした、より高い目線からの工場全体の最適化を実現できる自動化を、5年後、10年のスパンで検討していく必要があるのではないでしょうか。そう考えた時の選択肢はどうあるべきか、思い切った発想の転換が必要な時なのかもしれません。